PROJECTS
On this section of the site, you'll discover a curated list of the most impactful projects that have shaped my educational and professional career to date. These projects serve as a testament to my skills, dedication, and areas of expertise. For those interested in diving deeper into my academic achievements, I've also provided downloadable copies of my master's thesis and research papers. Whether you're a prospective employer, a fellow engineer, or simply intrigued by my work, this resource offers a comprehensive insight into my capabilities and contributions.
TECHNICAL UNIVERSITY OF MUNICH
Chair of Materials Handling, Material Flow, Logistics (fml)
POLITECHNIC UNIVERSITY OF VALENCIA
Chair of Applied Mathematics, E.T.S.I. Industrial Engineering School
SIEMENS LOGISTICS GMBH
Simulation Team
(SL AIR TI EN MS SIM)
Role:
Author
Development of an Optimization Method for the Automatic Layout Generation of Conveyor Systems
The development of efficient baggage handling systems is crucial for ensuring seamless travel experiences for passengers. A critical component of these systems is the conveyor system, which is pivotal in transporting baggage from check-in to the final destination. To improve the efficiency of conveyor systems, it is essential to design them to optimize their layout and maximize their throughput capacity.
This task, however, is challenging and time-consuming, as it requires extensive knowledge of the various components and constraints.
This research addresses that topic by developing an optimization method for the automatic layout generation of conveyor systems in baggage handling systems.
This approach involves using advanced algorithms to automate the process of conveyor system design, reducing the time and resources required for manual layout generation.



Master's Thesis


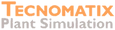

Semester Thesis

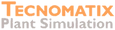
TECHNICAL UNIVERSITY OF MUNICH
Chair of Materials Handling, Material Flow, Logistics (fml)
Role:
Author
Development and Implementation of a Routing Algortihm for Heterogeneous Inbound Transport Systems
The aim of this work was the development of an algorithm that optimises order allocation and the routes to be taken in internal transport. Restrictions to be taken into account were, for example, the relationships between the different means of transport and transport units.
This algorithm was then implemented and evaluated in an existing model in Plant Simulation with SimTalk. The final solution was a combination of the Hungarian method and the 2-opt heuristic with the option to optimise travel times or distances to be traveled. These implementations resulted in significant improvements in system performance.
SUCCESSFULLY SUBMITTED TO I3M 2022
The 19th International Multidisciplinary Modeling & Simulation Multiconference

Bachelor's Thesis

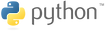
TECHNICAL UNIVERSITY OF MUNICH
Chair of Metal Forming and Casting (utg)
Role:
Author
Design, Implementation and Evaluation of a Software Tool for Partially Automated Optical Component Measurement
In the course of this work I developed a programme for manual and semi-automatic optical measurement of components by using simple mobile phone images. The programme contained a custom interface with the possibility of calibrating planes using Charuco boards and measurements in three-dimensional space. Measurements can be made either manually by drawing lines or by means of automatically generated borehole measurements. The implementation of the programme was done entirely in Python.


Team Lead for Simulation Projects for Airport Baggage Handling Systems
SD (Middle East) LLC
Simulation Team
SL ICS RC-AE EN
Role:
Team Lead

As the team lead, I am currently responsible for overseeing and executing all Siemens Logistics simulation projects in the Middle East. These responsibilities ensure the successful execution and delivery of high-quality 3D simulation projects, contributing to the overall efficiency and reliability of airport baggage handling systems in the region. The choice of simulation tool, whether AutoMod or Plant Simulation, is determined by the specific requirements and characteristics of each project.
Key processes to be carried out:
-
Model Creation: Developing comprehensive 3D simulation models for airport baggage handling systems (BHS) using AutoMod or Plant Simulation, including all PLC and IT logic
-
Model Optimization: Collaborating with other departments to refine and optimize the models, ensuring they meet the required performance standards.
-
Simulation Runs: Conducting multiple simulation runs to test various scenarios, assessing the efficiency, effectiveness, and robustness of the BHS under different conditions, such as high peaks or failures.
-
Simulation Report Creation: Compiling and presenting detailed simulation reports that document the findings, insights, and recommendations derived from the simulation runs.
-
Customer Training: Providing training to customers, ensuring they understand how to use and interpret the simulation models and reports effectively.
Creation of Custom Power BI Visuals for 3D Visualisations of Conveyor Systems
SIEMENS LOGISTICS GMBH
Simulation Team
SL AIR TI EN MS SIM
Role:
Responsible Person

Key processes carried out:
-
Development from Scratch: Creating the visuals from scratch using custom JavaScript code.
-
Data Integration: Enabling the visuals to link with additional data tables, allowing for filtering and automatic visualization of results within the 3D layout.
-
Interface Creation: Developing various interfaces to ensure compatibility with different tools used company-wide.
-
Dashboard Integration: Ensuring the custom visuals are ready to use and can be seamlessly included in any PowerBI dashboard.
I was responsible for the creation and implementation of a custom Power BI visual tailored for 3D visualizations of conveyor systems. These efforts ensured the seamless integration of advanced visualization capabilities into Power BI dashboards, significantly enhancing the analysis and presentation of conveyor system data used across the company.
ROLLS ROYCE MOTOR CARS LIMITED
Interior Manufacturing - Series Planning Department
Role:
Responsible Person
The scope of this year-long project ranged from initial requirements analysis through the entire procurement process to implementation and final evaluation of 2 new state of the art Drying Booths, meeting targets for quality, time, and cost. Concurrent budget of approx. £140k.
This project had a huge impact on all upstream and downstream processes due to a change in core drying technology and a major redesign of the layout.
Key processes carried out:
-
VSD of elaborated scenarios
-
Creation of business cases
-
Benchmark visits
-
Preparation of management status presentations
-
Planning and steering implementation of 2 bespoke designed state of the art Drying Booths
-
Elaboration of primary machine specifications, joint development of a technical solution through to completion of the procurement process
-
Update the layout of all affected processes to meet the new requirements
-
Managing all on-site suppliers during two 2-week implementation periods
-
Establishing a feedback loop and carrying out training sessions with the internal customer to guarantee full customer satisfaction

Realisation of a new state of the art Drying Booth
Implementation of a full masks Breathing Air Systems
ROLLS ROYCE MOTOR CARS LIMITED
Interior Manufacturing - Series Planning Department
Role:
Responsible Person
This project arose during my time as stand-in process specialist planner for the core processes of glue application and drying.
With the high health risks associated with spraying the adhesive onto the parts to be covered with leather, the employees need to be protected as much as possible. Due to the recent increase in volume and change in layout with the newly installed drying booths, the current breathing air system had to be replaced.
Key processes carried out:
-
Assessment of current safety measures in cooperation with the Health and Safety Department and external specialists
-
Internal benchmarking in different departments
-
Preparation of management status presentations
-
Planning and steering implementation of a full masks breathing air system including various air filters
-
On-site tests and approval of prototypes in coorperation with managers, Health and Safety Department and associates
-
Managing the whole procurement process of all necessary components
-
Leading the implementation of the breathing air system including all necessary adaptations to the existing infrastructure during normal production
-
Establishing a feedback loop and carrying out training sessions with the internal customer to guarantee full customer satisfaction

Stand-in Process Specialist Planner (PSP)
ROLLS ROYCE MOTOR CARS LIMITED
Interior Manufacturing - Series Planning Department
Role:
Process Specialist Planner (PSP)
During the last quarter of my internship in the Series Planning Department and due to the acquired expertise during all projects in these processes, I acted as stand-in process specialist planner (PSP) for the core processes glue application and drying.
Responsibilities:
-
Creation of work instructions and acting as a support function in the problem solving process
-
Continous improvements in material flow and layouts to reduce the 7 wastes
-
Gathering detailed glue specification information and benchmarking glue mixing possibilities to help improve this key process in the future
-
Implementation of a full masks breathing air system to tremendeously improve health and safety measures
